Maintaining a property or equipment is crucial for ensuring longevity, functionality, and safety. Effective maintenance helps prevent breakdowns, extends the lifespan of assets, and ensures that systems operate efficiently. Here’s a comprehensive guide on how to develop and implement a maintenance policy:
1. Objectives:
- Ensure Reliability: Keep systems and equipment in optimal working condition to prevent unexpected failures.
- Enhance Longevity: Extend the lifespan of assets through regular upkeep and timely interventions.
- Ensure Safety: Maintain safety standards to protect personnel and property.
- Optimize Performance: Ensure systems and equipment operate at peak efficiency.
2. Scope:
- Coverage: Define what is included in the maintenance policy (e.g., HVAC systems, plumbing, electrical systems, machinery, vehicles).
- Exclusions: Specify what is not covered by the policy (e.g., user-induced damage, external factors like natural disasters).
3. Maintenance Types:
- Preventive Maintenance:
- Routine Inspections: Schedule regular inspections and maintenance tasks based on manufacturer recommendations or historical data.
- Scheduled Tasks: Perform tasks such as cleaning, lubrication, and adjustments to prevent issues before they occur.
- Corrective Maintenance:
- Reactive Repairs: Address and repair issues as they arise, typically following a breakdown or malfunction.
- Diagnosis and Resolution: Identify the root cause of problems and implement corrective actions.
- Predictive Maintenance:
- Condition Monitoring: Use technology and data analysis to predict when maintenance should be performed based on equipment condition.
- Data Analysis: Monitor performance metrics and use predictive analytics to schedule maintenance before failures occur.
4. Reporting and Request Procedures:
- Reporting Issues:
- Mechanism: Provide clear channels for reporting maintenance issues (e.g., maintenance request forms, digital platforms).
- Response Time: Establish response timeframes based on the severity and urgency of the issue.
- Request Procedures:
- Documentation: Ensure all maintenance requests are documented with details about the issue, location, and any relevant observations.
5. Assessment and Planning:
- Initial Assessment:
- Inspection: Conduct an initial assessment to determine the nature and scope of the maintenance required.
- Prioritization: Prioritize tasks based on urgency, impact, and safety considerations.
- Maintenance Planning:
- Schedule: Develop a maintenance schedule that includes preventive, corrective, and predictive tasks.
- Resources: Allocate resources such as personnel, tools, and materials needed for maintenance tasks.
6. Execution and Procedures:
- Task Execution:
- Standard Operating Procedures (SOPs): Develop SOPs for routine maintenance tasks to ensure consistency and quality.
- Safety Protocols: Follow safety protocols and use appropriate personal protective equipment (PPE) during maintenance work.
- Quality Control:
- Inspection: Inspect completed maintenance tasks to verify that work meets quality standards and addresses the reported issues.
- Feedback: Collect feedback from personnel or users to assess the effectiveness of the maintenance.
7. Contractor and Service Provider Guidelines:
- Selection Criteria:
- Qualifications: Ensure contractors and service providers are qualified, licensed, and insured.
- Experience: Choose contractors with relevant experience and good references.
- Service Agreements:
- Contracts: Establish clear contracts or service agreements outlining scope, responsibilities, and performance expectations.
- Performance Monitoring: Monitor and evaluate contractor performance to ensure compliance with agreements.
8. Cost Management:
- Budgeting:
- Allocation: Allocate budget for routine maintenance, repairs, and unforeseen issues.
- Cost Control: Implement cost control measures to stay within budget while maintaining quality.
- Expense Tracking:
- Documentation: Track and document all maintenance-related expenses for analysis and reporting.
- Reporting: Regularly review and report on maintenance costs to identify trends and areas for improvement.
9. Documentation and Record-Keeping:
- Maintenance Records:
- Details: Maintain detailed records of all maintenance activities, including dates, tasks performed, and personnel involved.
- Historical Data: Use historical maintenance data to identify patterns, predict future needs, and improve planning.
- Documentation Systems:
- Digital Tools: Implement digital tools or maintenance management systems for efficient documentation and tracking.
10. Compliance and Regulations:
- Regulatory Compliance:
- Standards: Ensure maintenance activities comply with relevant local, state, and national regulations and standards.
- Inspections: Prepare for and facilitate inspections by regulatory bodies or auditors.
- Environmental Considerations:
- Sustainable Practices: Adopt environmentally friendly practices, including proper disposal of waste and use of eco-friendly materials.
11. Review and Continuous Improvement:
- Policy Review:
- Regular Updates: Regularly review and update the maintenance policy to reflect changes in regulations, technology, or operational needs.
- Continuous Improvement:
- Feedback Mechanism: Implement a system for gathering feedback from stakeholders to identify areas for improvement.
- Benchmarking: Compare maintenance practices against industry standards to identify best practices and areas for enhancement.
12. Training and Communication:
- Training Programs:
- Staff Training: Provide training for staff on maintenance procedures, safety protocols, and use of equipment.
- Contractor Training: Ensure contractors are trained on specific requirements and standards for the property or equipment.
- Communication:
- Policy Communication: Clearly communicate the maintenance policy to all relevant parties, including staff and contractors.
- Updates: Keep stakeholders informed about any changes to the policy or maintenance procedures.
Implementing a comprehensive maintenance policy helps ensure that all aspects of property or equipment maintenance are effectively managed, reducing the risk of unexpected failures, enhancing safety, and optimizing performance. Regular review and continuous improvement are key to maintaining an effective maintenance program.
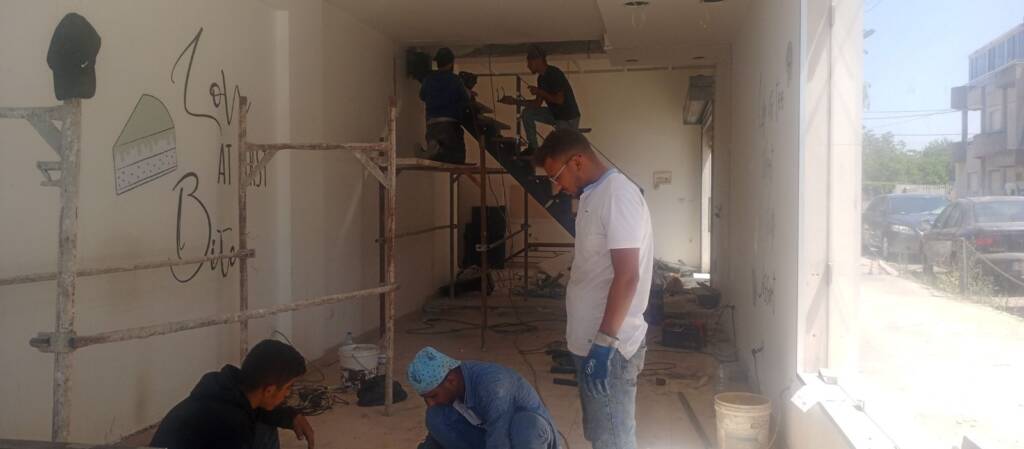
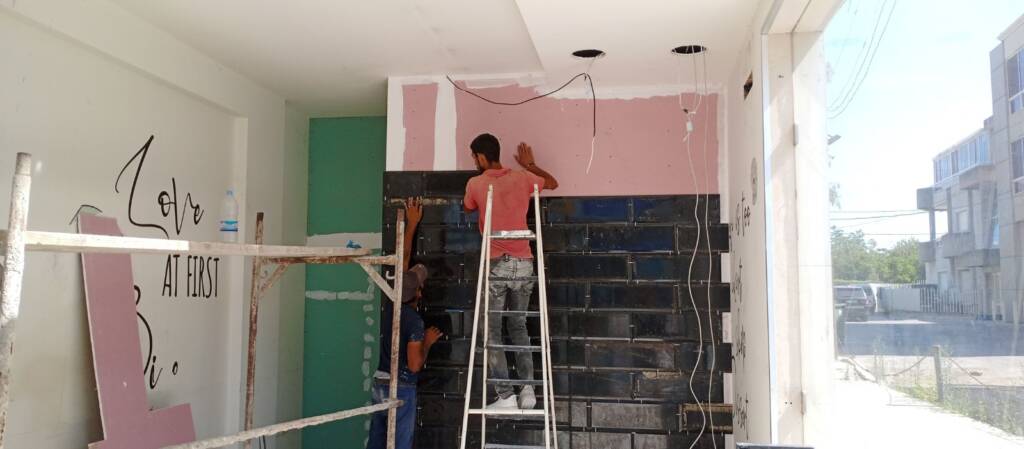
maintenance worker in amioun boneless